MES ile Üretim Hatalarında Kök Neden Analizi Nasıl Yapılır?
03.07.2025
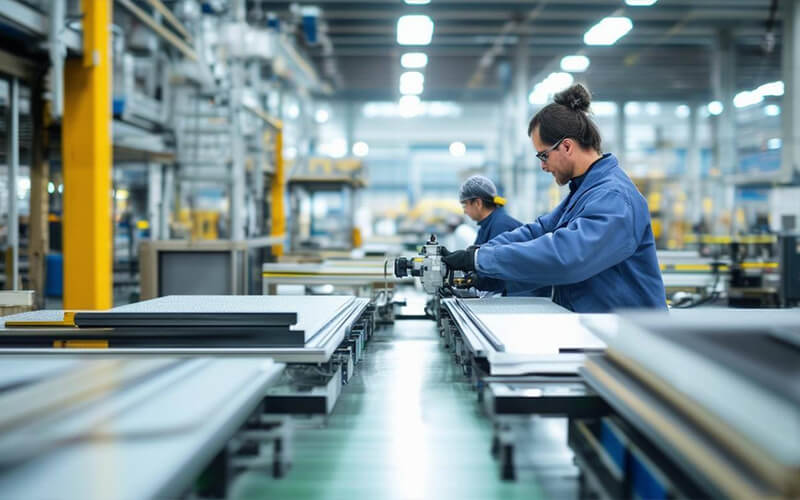
Üretim süreçlerinde meydana gelen hatalar, kalite kayıplarına, müşteri şikâyetlerine ve maliyet artışına neden olabilir. Bu hataları yalnızca düzeltmek değil, tekrar yaşanmamasını sağlamak da büyük önem taşır. İşte bu noktada kök neden analizi (Root Cause Analysis – RCA) devreye girer. MES (Manufacturing Execution System) yazılımları ise bu analiz sürecini dijital, sistematik ve etkili hale getirerek hataların arkasındaki temel nedenleri ortaya çıkarır.
Bu içerikte, MES sistemlerinin üretim hatalarında kök neden analizi sürecine nasıl katkı sağladığını adım adım inceleyeceğiz. Ayrıca, üretim kalitesini artırmak ve sürekli iyileştirme kültürünü yerleştirmek isteyen firmalar için bu entegrasyonun neden vazgeçilmez olduğunu açıklayacağız.
Kök Neden Analizi (RCA) Nedir?
Kök neden analizi, bir sorunun yüzeydeki belirtilerine değil, bu sorunun kaynağına odaklanan bir problem çözme yöntemidir. Amaç, hatanın oluşmasına neden olan temel faktörleri tespit ederek, kalıcı çözümler geliştirmektir.
RCA, genellikle “5 Neden Tekniği”, “Balık Kılçığı Diyagramı (Ishikawa)” ve “Pareto Analizi” gibi araçlarla desteklenir. MES yazılımları, bu analizlerin veri ihtiyacını karşılar ve süreci otomatize ederek hata çözüm süreçlerini hızlandırır.
MES Sistemleri ile Kök Neden Analizi Süreci
1. Gerçek Zamanlı Hata Verilerinin Toplanması
MES sistemleri, üretim hattındaki sensörler, makineler ve operatörlerden gelen verileri anlık olarak toplar. Hata oluştuğu anda, sistem otomatik olarak bu hatayı kaydeder.
Hatanın oluştuğu ürün, vardiya, operatör, kullanılan ekipman ve ortam koşulları gibi tüm bilgiler detaylı şekilde sistemde yer alır. Bu detaylar, kök neden analizinin ilk adımını oluşturur.
2. Hataların Kategorize Edilmesi
MES, oluşan hataları tiplerine göre sınıflandırır: ölçü hatası, montaj hatası, yüzey hatası, kalite dışı malzeme kullanımı gibi. Ayrıca her hata için şiddet, sıklık ve öncelik bilgileri sistemde saklanır.
Bu sınıflandırma, hangi hata türlerinin öncelikli olarak incelenmesi gerektiğini belirlemeye yardımcı olur. Pareto prensibi ile %80’lik hataların %20’lik nedenlerden kaynaklandığı kolayca tespit edilir.
3. Süreç Geri İzleme (Traceability)
MES sistemleri sayesinde her ürün, üretim sürecinde geçtiği tüm adımlarla birlikte izlenebilir. Hangi malzeme kullanıldı, hangi makinede işlendi, hangi operatör görev aldı gibi bilgiler geri dönük olarak erişilebilir durumdadır.
Bu izlenebilirlik sayesinde hata olan üründe hangi işlem veya ekipmanın hata kaynağı olduğu daha net şekilde belirlenebilir.
4. Operatör ve Kalite Ekibi Geri Bildirimleri
MES sistemi, hatayla ilgili operatörlerden veya kalite ekiplerinden açıklama istenmesini sağlar. Operatör arayüzü üzerinden “neden oluştu?”, “önceki benzer durumlarda ne yapılmıştı?” gibi sorulara cevap alınabilir.
Bu sayede sadece veriler değil, deneyime dayalı gözlemler de analiz sürecine dâhil edilir.
5. Otomatik Raporlama ve Görselleştirme
MES, kök neden analizine yönelik grafiksel ve istatistiksel raporlar sunar. Örneğin; zaman çizelgesi, neden-sonuç ilişkileri, en çok tekrar eden hata noktaları grafiklerle gösterilir.
Bu görseller, ekiplerin daha hızlı analiz yapmasına ve doğru kararlara ulaşmasına katkı sağlar.
6. Kök Neden Araçlarıyla Entegrasyon
İleri düzey MES sistemleri, kök neden analiz araçlarıyla entegre çalışabilir. “5 Why” (5 Neden) gibi yaklaşımlar sistem içinde uygulanabilir, süreç adım adım takip edilebilir.
Bu araçlarla kullanıcılar her hata için “Neden oldu?” sorusunu 5 katmandan sorgulayarak temel nedeni bulabilir.
7. İyileştirme Aksiyonlarının Takibi
Analiz sonrası alınan düzeltici ve önleyici aksiyonlar (CAPA), MES sistemi üzerinden tanımlanır. Her aksiyon için sorumlu kişi, planlanan tarih ve izleme mekanizması belirlenebilir.
Böylece sadece nedenler tespit edilmekle kalmaz, çözümlerin uygulandığından ve işe yaradığından da emin olunur.
MES ile Yapılan RCA’nın İşletmeye Katkıları
- Üretim hatalarının tekrar etmesi önlenir
- Ürün kalitesi artırılır, müşteri şikâyetleri azalır
- Arıza ve duruş kaynaklı kayıplar minimize edilir
- İnsan hatalarının kökenine inilip eğitim planları yapılabilir
- Standart dışı süreçler tespit edilip iyileştirilir
- Süreç sürekli iyileştirme kültürüyle desteklenir
RCA için MES Sisteminde Dikkat Edilmesi Gereken Özellikler
MES sisteminin RCA’ya etkin destek verebilmesi için bazı teknik yeteneklere sahip olması gerekir. Bunlar arasında:
- Geriye dönük izlenebilirlik (traceability)
- Gerçek zamanlı veri toplama ve kayıt
- Operatör ve kalite ekibiyle etkileşim arayüzleri
- İstatistiksel analiz ve grafik desteği
- Düzeltici/önleyici aksiyon modülü
- Kök neden araçlarıyla (Ishikawa, 5 Why, Pareto) entegrasyon
Eğer bu özellikler sistemde yer alıyorsa, kök neden analizi daha etkili, daha hızlı ve daha kalıcı hale gelir.
MES ve Yapay Zeka ile Geleceğin RCA Süreci
Gelişmiş MES sistemleri, yapay zeka algoritmalarıyla üretim verilerini analiz ederek olası kök nedenleri otomatik olarak önerme yeteneğine sahiptir. Bu sistemler, geçmiş hata verilerinden öğrenerek benzer durumlar oluştuğunda erken uyarı verebilir.
Makine öğrenmesi sayesinde MES, sadece geçmişi analiz etmez, aynı zamanda gelecekte oluşabilecek hataları da tahmin eder. Böylece kök neden analizi daha çok bir “öngörü yönetimi” halini alır.
Sonuç
Üretim hatalarında kök neden analizi, kalite ve verimlilik hedeflerine ulaşmak için kritik bir araçtır. MES sistemleri bu süreci dijitalleştirerek hem hızlandırır hem de doğruluğunu artırır. Gerçek zamanlı veri toplama, izlenebilirlik, operatör etkileşimi ve otomatik raporlama gibi özellikleriyle kök nedenlere ulaşmayı kolaylaştırır.
Kalıcı çözümler üretmek, tekrar eden hataları ortadan kaldırmak ve sürdürülebilir kalite yönetimi sağlamak isteyen işletmeler için MES tabanlı kök neden analizi vazgeçilmezdir. Dijital üretim çağında, sadece düzeltmek değil, hatayı bir daha yaşatmamak esastır.